Eco Corrugated Pack - Embrace Change, Embrace Green!
Mission:
We are dedicated to providing eco-smart eco-friendly printing and packaging machinery solutions, with the goal of becoming a pioneer in sustainable development. We firmly believe that taking care of the environment is the duty of every business, and through our efforts, we will work together to protect our magnificent Earth.
Eco Corrugated Pack provides custom printing and packaging machine solutions to high-quality corrugated carton box factories and offset printing carton manufacturers in the Middle East.
Eco Corrugated Pack assist you in building an eco-smart and eco-friendly factory.
ecocorrugated@gmail.com
Auto Feeder Diecutting Creasing Stripping Machine
1、Paper Feeding Unit
1) The enlarged paper feeding head (Feida head) has 9 suction nozzles applicable for paper in different thicknesses and 5 paper feeding nozzles which can be independently adjusted for parallel paper feeding. It also has 4 paper lifting nozzles which can move up and down in a large stroke especially applicable for small corrugated paper. The large power wind pump provides a high suction force. It can be conveniently adjusted; paper can be divided reliable, and it runs fast and stably.
2) By the special secondary paper feeding and preliminary paper stacking, the primary and secondary can be shifted to ensure uninterrupted paper feeding.
3) To improve the working efficiency, paper feeding and collecting are realized by Taiwan WANSHSIN dual-speed reduction motor which provides a long service life and a high torsional force, and it saves time due to its high lowering speed.
2、Paper Conveying Unit
1) The paper conveying part is made of stainless steel plate to prevent rust and provide stable and correct paper conveying.
2) Paper is positioned by a pushing unit and a pulling unit which can be shifted conveniently for different specifications of paper.
3、Die-cutting Unit
1) The cast wall plate is rejected because of its low pulling force but high deformation, and steel wall plate is applied like Japan machines. The pulling force is enlarged, i.e. the pressing force is enlarged, and it becomes firm and endurable without any deformation.
2) This machine is upgraded to a brand high level by the automatic pressure regulation and automatic front scale regulation. The addition of this function upgrades it into a convenient and favorable digital device with high controlling speed.
3) The oil route is forcibly lubricated by a HP oil pump as made in Taiwan to reduce wearing, an oil cooler is added to cool the lubricating oil, and the main chain is lubricated timely to improve the operation efficiency.
4) The novel transmission mechanism provides high speed die-cutting, and the highly precise swing link platform improves the padding speed (almost without padding), as it is known the pressure can be hardly balanced in most of other common machines.
5) The pneumatic plate locking unit can fix the upper frame more firmly and faster. In our die-cutting machine, the front, back, left and right are pneumatically locked simultaneously to realize a high correctness and a high speed. However, common machines are tightened by screws.
6) The paper holding rack chain is imported from Germany, which provides a long service life and a stable die-cutting precision.
7) The Taiwan intermittent mechanism is the main transmission part of the die-cutting machine, and it improves the die-cutting speed and precision and reduces the device noise, while the speed and precision cannot be realized by any domestic mechanism.
8) The torque limiter is equipped with overload protection. The primary and secondary units can be separated at any overload to ensure the machine can be operated safely. The Italia pneumatic brake and clutch with Japan SMC rotary joint comply with the European standard. They provide fast clutching, high and stable force, long service life and low noise.
4、Paper Stripping Unit
1) By the one-time stripping system, all irrelative paper scrapes and waste edges (except the held margins) can be stripped in die-cutting.
2) The up, down and middle die cam tri-link transmission system is stable, harmonious, and correct for high power and fast loading, unloading and calibrating.
3) The stripping frame is pneumatically lifted with a centering unit, and it can be operated easily to shorten the preparation time.
4) The preliminarily loading platform is equipped with a centering unit to facilitate the mounting of stripping plate.
5) The stripping process is reasonably designed to eliminate the defect of low speed and plate deviating during stripping.
5、Paper Collecting Unit
1) Paper can be collected automatically and orderly.
2) The efficiency is improved by an uninterrupted paper collecting grid plate, and when paper is stacked to the specified height, the paper collecting grid plate will be replaced by another plate for uninterrupted paper collecting.
3) By the pneumatic sampling, the die-cut paper can be conveniently inspected at any time.
6、Electrical Control Unit
1) The electrical control system is Japan Omron PLC computer automatic control for fully detecting and controlling, and the Japan TOSHIBA frequency converter with Taiwan main motor provides high power for paper feeding, paper conveying, die-cutting, and paper collecting.
2) The human-machine interface can display various working conditions, indicate fault positions and give solutions.
3) The machine is equipped with various safety protection units. A visible and audible alarm will be given at any fault, and the machine will be automatically shut down to protect personal and device safety.
Specifications sheet
Model |
ECO-1080E |
Max.paper size |
1080×780mm |
Min.paper size |
400×370mm |
Max.cutting size |
1050×750mm |
Max.cutting speed |
7500s/h |
Max.Stripping speed |
6500s/h |
Sheet thickness |
Corrugated board: ≤4mm
Cardboard:0.1-3mm |
Max.pressure |
320 Tons |
Max. Feeding Pile |
1800mm |
Max. Delivery Pile |
1600mm |
Total power |
19.8KW |
Net weight |
18.5 Tons |
Overall dimension |
8350×3950×2360mm |
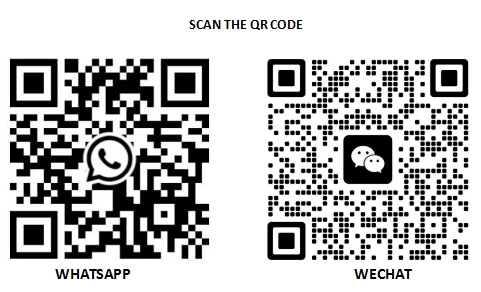